The Power of Telematics and Fleet Management for Enhanced Efficiency
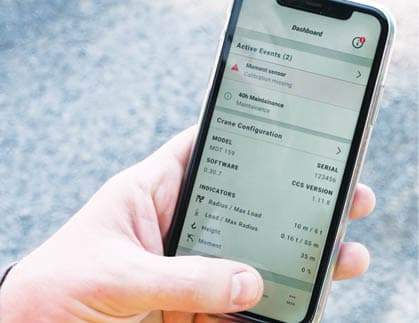
Telematics systems facilitate advanced fleet management by bringing information to crane users in real time, noted Markus Paulini, manager telematics mobile cranes, at Manitowoc. “Customers know exactly what’s going on with their cranes,” he said. “Users and dealers can manage a single crane or a whole fleet while covering both their needs.”
Paulini added that telematics’ insight gives immediate feedback on a crane’s performance. “Connectivity with cranes improves operations and streamlines service and maintenance,” he said. “It promotes optimized troubleshooting by allowing you to quickly understand the status of a crane, avoiding wasted time on the job site.”
Lance Rydbom, director of product management and engineering for Tadano Americas, said tying telematics to a company’s fleet management tools lets a company monitor the location of its cranes and allows owners to improve utilization by seeing any gaps in their fleets. “Monitoring maintenance intervals more accurately by tracking the number of hours on critical components reduces downtime by letting service technicians see what the operator sees,” he added.
“Thanks to cutting-edge communications technology, real-time technical and location information, and even data related to productivity and maintenance, rental companies and contractors can save time and costs while improving efficiency,” said Joseph Patton, sales manager at Linden Comansa America. “Telematics facilitates a comprehensive approach to fleet management, including analysis and verification of working hours, productivity, and crane lifetime.”
Patton added, “Through telematics, including integration with third-party platforms and customized reporting, it is possible to reduce operating and service costs, and maximize fleet efficiency and profitability.”
Telematics data on machine location, daily usage statistics, fuel levels, and crane setup, among other things, is assisting users with full fleet awareness, noted Wolfgang Beringer, marketing and communications, Liebherr-Werk Ehingen GmbH. “All of that facilitates operations and supports accuracy,” he said.
“Telematics systems can transform maintenance by providing near-real-time data to crane owners,” said Pat Collins, director of marketing, Link-Belt. “It can allow fleet managers to improve logistics by enabling companies to be more precise in what actually requires maintenance at a point in time, saving time and money. In addition there is the machine troubleshooting and diagnostics aspect in some cases. Telematics systems play a crucial role in equipment utilization and reduced downtime, resulting in better overall decision-making in the management of cranes.”
Advanced Technologies
Tadano offers two telematics systems for its cranes, reported Rydbom. One is the IC-1 Remote for machines that use the IC-1 Plus operating system.
The other is Hello-Net, which provides machinery management information, such as activities, locations, and maintenance status.
IC-1 Remote taps into more than 150 data points from the IC-1 Plus control system, and both systems can set up notifications for various customizable alerts.
Comansa’s Crane Mate system provides real-time technical information, location, and alerts, as well as productivity and maintenance parameters for the manufacturer’s tower cranes.
Features of the fleet management and crane monitoring system, noted Patton, include crane location, operating and idle time, load cycles, wind alerts, and work and maintenance plans for the machines and projects.
Crane Mate monitors more than 100 crane parameters, including trolley-hook position, momentum limiters, load limiters, and wind speed.
The system also enables rental period registration for cranes and projects, uploading of manuals and technical data sheets, configuration of alerts and error warning messages, and customized reports.
The solution also can send data to a customer’s fleet-management platform.
The iCraneTrax solution powered by Link-Belt’s Pulse crane control provides up-to-date information, such as crane location, operating hours, fuel usage, operating times of functions, idle time vs. load time, and other essential data, related Collins.
Manitowoc’s Grove Connect system is now standard on new all-terrain cranes that have the company’s Crane Control System (CCS). When used on Potain tower cranes, the telematics system is called Potain Connect.
Manitowoc provides free use of the standalone systems while a crane’s in warranty, then afterward offers them by subscription.
Grove Connect and Potain Connect each provide a maintenance plan that predicts remaining operating hours or mileage based on the
crane’s age.
The Connect platforms’ intuitive interfaces give Manitowoc customers access to a variety of crane control and management functions that drive proactive remote maintenance and guide troubleshooting, noted Paulini.
Users of Potain Connect can also improve the security and sustainability of their cranes by making adjustments remotely.
That remote capability minimizes service-tech travel and avoids usage that affects safety.
Liebherr’s solution for its mobile and crawler cranes shows the machine’s location and also displays a range of real-time data, such as fuel consumption, current wind speed, the weight of the load on the hook, machine hours, and mileage. It all helps with crane maintenance.
Trina Baughman, product manager of digital services for the mobile and crawler cranes division of Liebherr USA Co., said that some machines produced in 2023 are factory equipped with a standard modem that will transmit data including fuel level, current crane condition, setup codes, and current wind readings if wind sensors are installed on the machine.
Baughman added that Liebherr will offer a retrofit kit for cranes made as long ago as 2018.
“The system lets users define an area on a map, such as a construction site, and a time period,” Baughman said. “Whenever the machine is in the defined area, data is available to analyze things like a particular crane’s operating hours at the selected site during the defined period, how much fuel it consumed, and even how much emissions it generated. The data forms the basis for reports and helps the customer manage its fleet as economically as possible.”
The company’s performance platform is accessed through the MyLiebherr customer portal.
There, owners and operators can register cranes, download operating instructions, and see machine data.
Users on the platform’s updated start page can see all the machines in their fleet and navigate directly to the desired unit.
Looking Ahead
Manitowoc, related Paulini, is using its CCS architecture and software development skill to build crane-specific menus and visual adaptions for new telematic applications.
“We are also in the process of creating a utilization report that enables precise invoicing and increases transparency for operations at job sites,” he said.
“We see this as having appeal for rental companies,” Paulini continued. “Other functionality, such as reporting wind speed data, can help customers and operators on a site, and we are working on enabling APIs for even stronger collaboration capabilities.”
“Along with the Link-Belt Pulse crane control system,” said Collins, “the future of telematics is focused on additional built-in data points. Over time, this will increase the level of detail for reporting and operations.”
For Liebherr, the company’s newest telematics and data management system is the beginning of many future digital services.
Continued plans include incorporating custom reports for specially defined construction sites, geofencing, and service notifications, noted Baughman. “Also coming soon is a platform that will deliver live crane data to both office staff and operators,” she said.
Xavier Claeys, director of digital innovation for Manitowoc’s Potain tower cranes, said a new app-based digital platform for remote monitoring, servicing, and management of Potain models is under development.
“Of course, connectivity is nothing new,” he said. “We have had tools providing remote information on our tower cranes to technicians and customers for about 10 years. But it’s only in the last two to three years that we have seen significant interest from customers in having a single, comprehensive platform for remote monitoring, servicing, and crane management.”
Claeys added, “Facing pressure to contain cost and limit environmental impact, customers are starting to recognize the power of data to improve uptime, efficiency, and productivity. Data is not a solution by itself. What matters is how you encapsulate data into a usable system. With these new tools, crane operators and owners are empowered to develop their business based on the information they get from their cranes.”
Full information and details on telematics systems offered by crane manufacturers is available online:
• Comansa Crane Mate: https://northamerica.comansa.com/en/crane-mate
• Liebherr: https://www.liebherr.com/en/usa/products/mobile-and-crawler-cranes/service/performance-coming-soon.html
• Link-Belt: https://www.icranetrax.com/LBCE/
• Manitowoc (Grove and Potain): https://www.manitowoc.com/support/grove-connect-potain-connect
SIDEBAR:
Integrating Telematics and Fleet Management
Telematics systems have been logging data for fleet managers for years, noted Matt Reinhart, senior marketing manager, Fleet Cost & Care, in an online article.
However, the information is relatively static when it isn’t incorporated into a larger system that allows reporting and analytics.
“Integrating your telematics data with a comprehensive fleet management system allows fleet managers to turn static data into actionable information,” according to Reinhart.
Using telematics to track fleet performance is an essential first step, but it needs a centralized fleet management system to turn data into action.
In a series of questions and answers, Reinhart explained how the integrated capabilities can benefit crane operators:
How Does Telematics Help Manage Fleets Across Job Sites and Regions?
Currently, many GPS providers enable fleet managers to track their units across job sites, projects, and regions, and some have started working toward a more granular approach by incorporating unit components.
This is being achieved through a variety of technologies including long-life battery powered systems that enable tracking with considerable accuracy.
Fleet management software acts as a hub for this data, integrating unit and personnel information for scheduling, inventory tracking, and maintenance. It allows you to measure asset utilization vs. cost.
How Can Telematics Systems Help with Service and Preventive Maintenance? Can They Monitor a Unit’s Status During Repair?
Most providers offer some form of maintenance tracking, but they do not have or support a full maintenance system.
For example, one provider may offer a solution for identifying a deficiency through their Daily Vehicle Inspection Report (DVIR),
However, this information is relatively static and still requires verbal communication or active monitoring of a web application to identify and resolve issues.
A fleet management system offers end-to-end maintenance tracking from deficiency identification, automated communication back to a work order system, work order generation, and labor and cost tracking.
How Can Telematics Reduce Fleet Costs and Improve Margins?
Telematics can reduce costs through improved transparency in many areas, such as fuel and driver safety.
Keeping up with preventive maintenance can save a lot of money on repairs and extend the life of a unit.
Increased margins come through reduced costs.
Comprehensive reports from an integrated fleet management system bring telematics data and fleet costs under one umbrella. That full picture of profitability enables informed decisions on capital investments.
How Can Telematics Improve Personnel and Document Management?
Telematics can give management insight into employee performance, work duration, and safety.
Fleet management software lets users see, directly on the job schedule, how much time is remaining for cycle time, driving time, and on-duty time each day.
E-tickets and checklists let users list issues identified on the job, track signatures, and account for personnel.
What Will Telematics Systems Track in the Future?
Telematics providers are constantly coming up with new ways to track data, including fluid levels, engine diagnostics, seat occupation, seat belt use, video camera captures, and others.
As these capabilities become more widely adopted, we will see data points coming into a centralized management system.
There they can be tracked and reported on in a multitude of ways to inform management and help make critical business decisions.
Telematics provide valuable but standalone data to siloed departmental users, Reinhart noted.
When fleet management systems are integrated with telematics, they can bring together critical data for improving fleet productivity and reducing operational costs.